放電加工と聞いて皆さんはどんな加工を思い浮かべますか?
放電と言えば雷などのように電気が放たれることですよね。この放電のメカニズムを金属加工に応用したものが放電加工です。放電加工は、簡単に言うと電気のエネルギーで金属を溶かす加工になります。今回は、放電加工の3つの種類と特徴についてご紹介していきます。
放電加工とは
放電加工とは、簡単に言うと電気のエネルギーで金属を溶かす加工です。銅やグラファイト、真鍮などを工具電極とし、加工物と電極との間に生じる放電作用によって加工物を少しずつ溶かしていきます。放電加工は、EDM(Electrical Discharge Machining)とも呼ばれています。
放電加工の種類と特徴
放電加工には、「型彫り放電加工」「ワイヤーカット放電加工」「細穴放電加工」の3つの加工方法があります。
型彫り放電加工
型彫り放電加工はまず銅やグラファイト等を材料にして工具電極を作ります。
その出来上がった工具電極の形を加工材料に転写する加工方法です。
ワイヤーカット放電加工
ワイヤーカット放電加工は、0.2mmほどの真鍮製のワイヤー線に電気を流して、その時に発生する熱で金属を切る加工方法です。ワイヤーカット加工についてはこちらの記事で詳しく紹介しています。
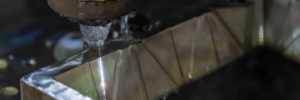
細穴放電加工
細穴放電加工は、棒状の電極を使いドリル加工では困難な極小の穴や高硬度の材料に穴をあける加工方法です。
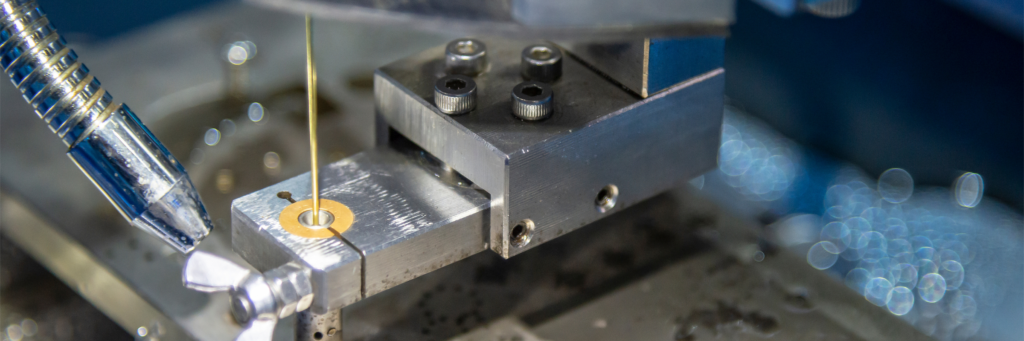
放電加工のメリット・デメリット
メリット
①電気を通す材料なら硬さや厚さに関係なく加工できる。
②切削加工と比べ、バリの発生もなく高精度で加工が可能。
③加工物と非接触の為、負荷をかけずに加工できる。
最大のメリットは、硬い素材を加工できることだと思います。さらに、非接触で加工ができる点ため、斜めの面でも段差があっても関係なく加工できる点も大きなメリットと言えます。
デメリット
①少しずつ溶かしながら切断するため、加工速度が遅く、大量生産には不向き。
②電気を通さない材料は加工できない。
③型彫り放電加工は工具電極を製作する必要があるためコスト、製作時間がかかる。
最大のデメリットは加工速度が遅いことです。少しずつ溶かしながら加工していくため、大量生産には向いていません。電気を通さない材料には放電加工ができないのも欠点ですね。型彫り放電加工に使用する電極を作る場合は切削加工などを用いるため、その分のコストもかかってくることを考えておく必要があります。
放電加工に使用する電極について
銅
銅は最もコストが安く、電極として一番多く使われている材料。電気抵抗が少なく熱伝導率は高いですが、耐熱性が低いことが弱点です。電極が消耗しやすいため、荒取り用と仕上げ用に同じ電極を複数用意する場合が多いです。
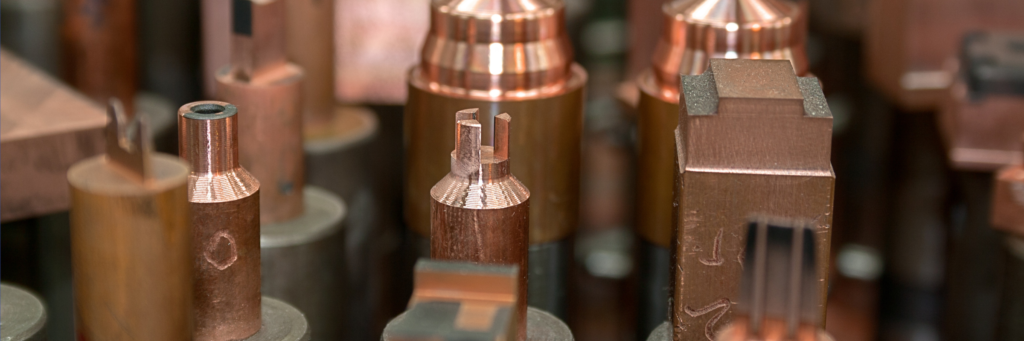
グラファイト
グラファイトは銅とは反対で熱に強く、電極の消耗が少ないのが特徴です。銅と比べると加工スピードも高いです。ただし、加工にはグラファイト加工機と呼ばれる専用の機械が必要になります。
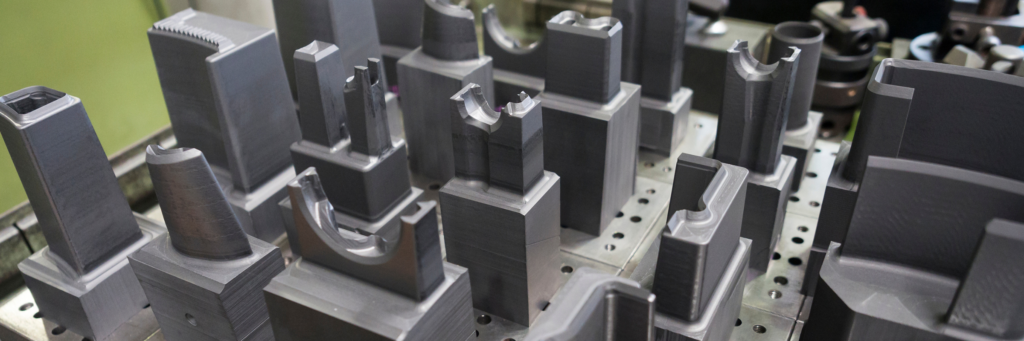
真鍮
ワイヤーカット加工や細穴放電加工では真鍮を使用します。ワイヤーカットでは、Φ0.02mm~Φ0.3mmのワイヤー線を使用し、細穴放電加工では、あける穴に応じた太さのパイプ電極を使用します。
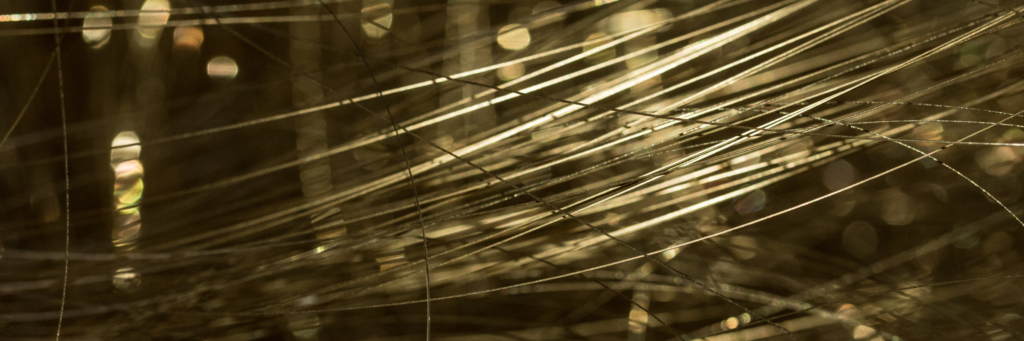